Ibanez Cavity Depth
(c38) Guitar Termolo Cavity Back Plate Cover for Ibanez RX Series Black ABS. 3.8 out of 5 stars (4) Total Ratings 4, $5.50 New. 4pcs Neck Mounting Bushings Ferrules and 4pcs Screws Fit Ibanez GuitarC Chrome. 4 out of 5 stars (2) Total Ratings 2, $3.99 New. The following is a list of neck types that Ibanez uses or has used for its electric guitar models, including the neck dimensions. The years indicate the period the neck of that description was used. Note that a neck type can change over the years. Dimensions are from tables provided by Ibanez in their catalogs as well as on their website. For a similar list of neck dimensions for acoustic. Typical setup for 9-42 gauge strings using the typically found 52mm springs found in most Ibanez. For 8's I'll usually use 2 springs in an arrow formation, outside holes on the trem block to the 2 inner hooks on the claw. For 10 gauge sets I always add a 4th spring although 3 will work if you have room to screw the claw far enough. This guitar still functioned acoustically, but had a smaller resonant cavity inside, which makes less sound emit from the f holes. Gibson first manufactured this variant in 1958. It is commonly referred to as a semi-hollow body guitar, because of the smaller, less open body. Rickenbacker also began making semi-acoustic guitars in 1958. So I bought a covered setof Dimarzios for my Ibanez RG921, and just discovered they won't fit into the direct mount cavity. My tech wants $60 per pickup installation/routing.
A semi-acoustic guitar or hollow-body electric (and in some cases, thinline) is a type of electric guitar that originates from the 1930s. It has both a sound box and one or more electric pickups. This is not the same as an acoustic-electric guitar, which is an acoustic guitar with the addition of pickups or other means of amplification, added by either the manufacturer or the player.
History[edit]
In the 1930's, guitar players found that the absolute sound of the guitar was insignificant when compared with other instruments at the time such as the drums. Guitar manufacturers aimed at increasing the sound level produced by the instrument.[1] A range of designs developed by companies such as Gibson, Rickenbacker and Gretsch focused on amplifying a guitar through a loudspeaker. In 1936, Gibson introduced their first electric guitars, the ES-150s (Electric Spanish Series) were the first manufactured semi-acoustic guitars.[2]
Gibson based them on a standard production archtop, with f holes on the face of the guitar's soundbox. This model resembled traditional jazz guitars that were popular at the time. The soundbox on the guitar let limited sound emit from the hollow body of the guitar. These guitars, however, could be electrically amplified via a Charlie Christian pickup, a magnetic single-coil pickup that converted the energy of the vibrating strings into an electrical signal.[2] The clear sound of the pickups made the ES series immediately popular with jazz musicians.[1] The first semi-acoustic guitars are often thought of as an evolutionary step in the progression from acoustic guitars to full electric models.
However, Gibson made the ES-150 several years after Rickenbacker made the first solid-body electric guitar. The ES series was merely an experiment the Gibson company used to test the potential success of electric guitars. The experiment was a successful financial venture, and the ES series is often referred to as the first successful electric guitar. The ES-150 was followed by the ES-250 a year later, in what became a long line of semi acoustics for the Gibson company.[3]
In 1949 Gibson released two new models: the ES-175 and ES-5. These guitars came standard with built-in electric pickups and are widely considered the first fully electric semi-acoustic guitars.[4] Prior models were not built with pickups; rather, they came as attachments. As the production and popularity of solid body electric guitars increased, there was still a market of guitar players who wanted to have the traditional look associated with the semi-acoustic guitars of the 1930s but also wanted the versatility and comfort of new solid body guitars. Several models, including the ES-350T by Gibson, were made in the 1950s to accommodate this growing demand by including a more comfortable version of the archtop model.[2]
Gibson and other makers followed these variations with an entirely new type of guitar that featured a block of solid wood between the front and back sections of the guitars cutaway. This guitar still functioned acoustically, but had a smaller resonant cavity inside, which makes less sound emit from the f holes. Gibson first manufactured this variant in 1958. It is commonly referred to as a semi-hollow body guitar, because of the smaller, less open body.[2]
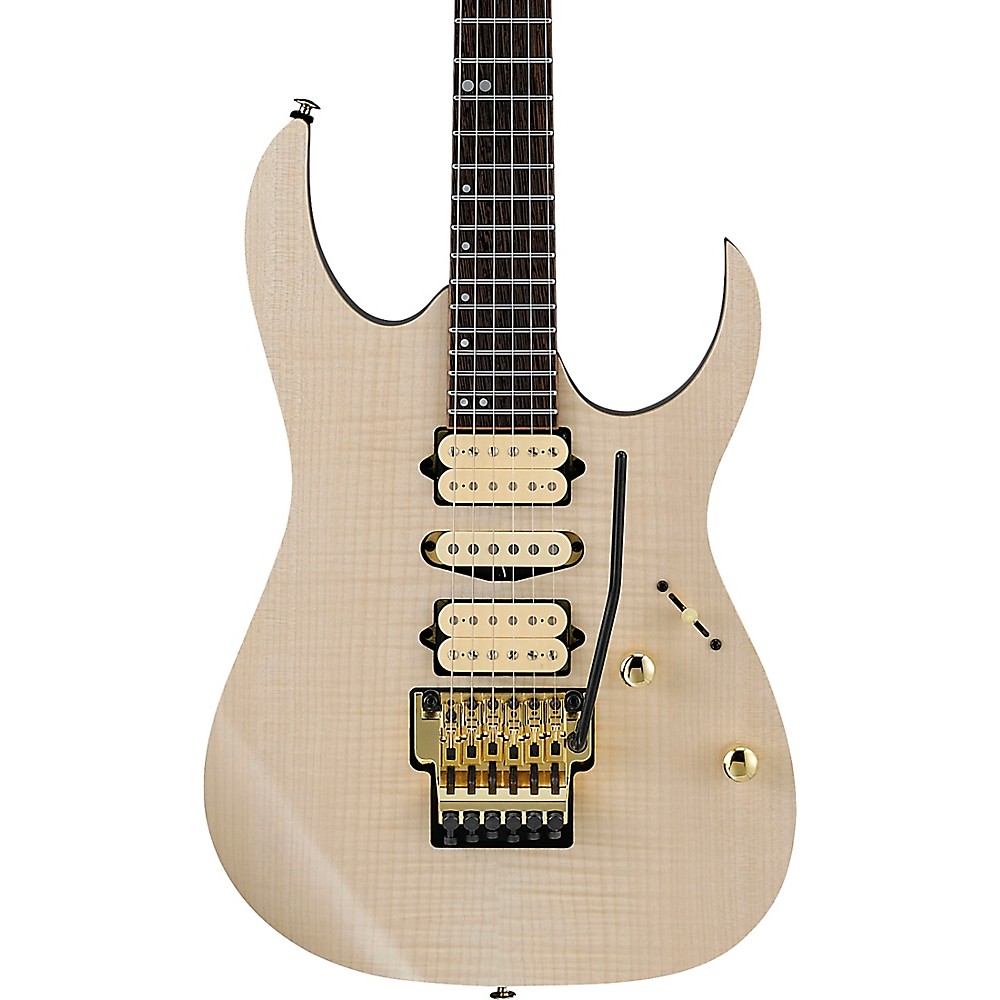

Rickenbacker also began making semi-acoustic guitars in 1958. When the company changed ownership in 1954, they hired German guitar crafter, Roger Rossmiesl. He developed the 300 series for Rickenbacker, which was a wide semi-acoustic that did not use a traditional f hole. Rather it used a sleeker dash hole on one side of the guitar, the other side had a large pickguard. This model boasted a modern design with a unique Fireglo finish. It quickly became one of Rickenbacker's most popular series and became a strong competitor to Gibson's models.[5]
In addition to the main model variants of the guitar, Gibson made several small changes to the guitar, including a laminated top for the ES-175 model and mounted top pickups for general use on all their models, as opposed to Charlie Christian models from the 1930s.[1] While Gibson provided many of the innovations in semi-acoustic guitars from the 1930s to the 1950s, there were also various makes by other companies including a hollow archtop by Gretsch. The 6120 model by Gretsch became very popular as a rockabilly model despite having almost no technical differences from Gibson models.[6] Rickenbacker was also a prominent maker of the semi-hollow body guitar. Gibson, Gretsch, Rickenbacker, and other companies still make semi-acoustic and semi-hollow body guitars, making slight variations on their yearly designs.
Usage[edit]
The semi-acoustic and semi-hollow body guitars were enjoyed for their clean and warm tones. This led to widespread use throughout the jazz communities in the 1930s. As new models came out with sleeker designs, the guitars began to make their way into popular music. The guitar became used in pop, folk, and blues. The guitars sometimes produced feedback when played through an amplifier at a loud level. This made the guitars unpopular for bands that had to play loud enough to perform in large venues. As rock became more experimental in the late 60s and 70s, the guitar became more popular because players learned to use its feedback issues creatively; One example is Ted Nugent, who primarily plays the semi-acoustic Gibson Byrdland.
Semi-hollow guitars share some of the tonal characteristics of hollow guitars, such as their praised warmth and clean tone. However, the addition of the central block helps to manage feedback and allows the guitar to be played normally at higher gain and higher volume. Semi-hollow guitars with a central block are also more durable than fully hollow guitars, whose sound is particularly popular with jazz, blues, rockabilly and psychobilly guitarists.
Today, semi-acoustic and semi-hollow body guitars are still popular among many artists across various genres. Examples include Dan Auerbach of The Black Keys, renowned jazz guitarist George Benson, John Scofield, multi-instrumentalist Paul McCartney and former Guns N' Roses member Izzy Stradlin. Famous guitarists of the past who have used semi acoustic guitars include John Lennon of the Beatles and B.B. King, both of whom have had signature semi-acoustic models released. Semi-acoustic guitars have also been valued as practice guitars because, when played 'unplugged,' they are quieter than full acoustic guitars, but more audible than solid-body electric guitars because of their open cavity. They are also popular because the cavities reduce the weight of the guitar.[7]
With most solid-body guitars, the electronics are accessed, repaired, or replaced by removing either the pick guard or an access panel on the back of the guitar’s body. In a semi-acoustic guitar, where there is no solid body to create a chamber to house the electronics, these components are pushed or pulled through the lower f-hole of the guitar’s body.[8]
Variations[edit]
Other semi-acoustic instruments include basses and mandolins. These are similarly constructed to semi-acoustic guitars, and are used in the same ways and with the same limitations.
Some semi-acoustic models have a fully hollow body (for instance the Gibson ES-175 and Epiphone Casino), others may have a solid center block running the length and depth of the body, called semi hollow body (for instance the Gibson ES-335).
Other guitars are borderline between semi-acoustic and solid body. For example, some guitars have chambers built into an otherwise solid body to enrich the sound. This type of instrument can be referred to as a semi-hollow or a chambered body guitar. Players disagree on exactly where to draw the line between a constructed sound box and a solid wooden body (whose construction also affects the sound according to many players). Any of the following can be called semi-acoustic:
- Instruments that start from a solid body blank that has been routed out to make a chambered body guitar, such as the Fender Telecaster Thinline
- Instruments with semi-hollow bodies constructed from plates of wood around a solid core, with no soundholes, such as the Gibson Lucille or Brian MayRed Special[9]
- Instruments with a solid core but hollow bouts and soundholes (usually f-holes), such as the Gibson ES-335.[10] In these, the bridge is fixed to a solid block of wood rather than to a sounding board, and the belly vibration is minimised much as in a solid body instrument
- Thin-bodied archtop guitars, such as the Epiphone Casino, that have a sounding board and sound box, but purely to modify the sound transmitted to the pickups—still intended as purely electric instruments because of their weak acoustic sound
- Full hollowbody semi-acoustic instruments, often called Jazz guitars, such as the Gibson ES-175; these have a full-size sound box, but are still intended to be played through an amplifier.
Sound Hole Variations:
- Many hollow body guitars, both semi and full have Cat-Eyed or Cat Eye sound holes which are shaped like the eye of a cat instead of the traditional F Holes.[11]
Gallery[edit]
B. B. King's Lucille
The Rickenbacker 330 JG
References[edit]

- ^ abcIngram, Adrian, A Concise History of the Electric Guitar, Melbay, 2001.
- ^ abcdHunter, Dave, The Rough Guide to Guitar, Penguin Books, 2011.
- ^Miller, A.J., The Electric Guitar: A History of an American Icon, Baltimore, MD, Smithsonian Institution, 2004.
- ^Martin A. Darryl, Innovation and the Development of the Modern Six-String, The Galpin Society Journal (Vol. 51), 1998.
- ^Rogers, Dave, 1958 Rickenbacker 330, http://www.premierguitar.com/Magazine/Issue/2009/Aug/1958_Rickenbacker_330.aspx, accessed 11 December 2011.
- ^Carter, William, The Gibson Guitar Book: Seventy Years of Classic Guitar, New York, NY, Backbeatbooks, 2007.
- ^Hunter, Dave (August 2012). '5 Things About Hollow, Semi-Acoustic, and Chambered Electric Guitars'. Guitar Player. 46 (8): 146.
- ^'Wiring A Hollow Body Guitar the Easy Way | Seymour Duncan'. www.seymourduncan.com. Retrieved 2016-02-16.
- ^Hunter, Dave (2010). Star Guitars: 101 Guitars that Rocked the World. Voyageur press. p. 22.
- ^Russell, Daniel A.; Haveman, Wesley S.; Broden, Willis; Weibull, N. Pontus (2003-03-20). 'Effect of body shape on vibration of electric guitars'. The Journal of the Acoustical Society of America. 113 (4): 2316–2316. doi:10.1121/1.4780761. ISSN0001-4966.
- ^Brown P., Newquist H.P. (1997). Legends of Rock Guitar: The essential reference of rocks greatest guitarists. Hal Leonard Corporation. ISBN0793540429.
Build an Electric Guitar - Without the Fancy Tools
Ibanez Cavity Depth Scale
Wood Selection
The most common body woods for electric guitars are mahogany, alder, walnut and swamp ash. Swamp ash is my favourite body wood due to its lightweight and great mid-range tone. You will need two pieces of 8/4 stock for the body, at least 21'x 7 ½' finished dimensions.
The neck is most commonly made from hard maple or mahogany. Walnut is also used, giving a more complex acoustic-like tone. Neck wood needs to be straight grained and free of knots. Quarter sawn is best but flat sawn is also used. You can also use flat sawn stock and laminate it to get a quarter sawn neck blank; this is the method I use. A laminated neck is stiffer and more stable than a one-piece neck. You may use different combinations of wood to make different patterns of laminations if you wish. Rough neck stock should be about 36'x 5' x 4/4 and the finished thickness of the neck blank is 21mm.
The fingerboard should be quarter sawn with straight grain, free of knots and heavy figure (an exception to this is bird’s eye maple). I recommend using rosewood, ebony or Ziricote. If you decide to go with a maple fingerboard it will need to be finished with a lacquer or urethane clear coat before the frets are installed. If left unfinished, maple fingerboards will quickly become dirty and stained with frequent playing.
For this project I suggest using a pre-slotted and radiused fingerboard from Stewart MacDonald. The spacing of the frets is too critical to risk. This will save you from having to buy somewhat costly fret scale templates, radiused sanding blocks and a fret slot saw.
Start by Making the Templates
While you’re building this guitar be sure to reference the hardware you plan on using when routing all the cavities. Make a point of obtaining all hardware before you start the project so there are no surprises later.
Unlike most guitars, this one is made using basic woodworking tools. No fret saws, gauged nut files or any other fancy tools here. A router will do most of the work, with a bandsaw, drill and some basic sanding equipment filling in when needed.
Master templates – The first thing to do is make a master neck and body template from ¾' MDF. For this style of guitar the neck is 1 ¾' wide at the nut and 2 5/16' at the heel. The distance from the end of the neck to the nut is 18 ¼'. The total length of the neck is about 24 ½', though the length may vary depending on your headstock design. The body is about 18' long and 13' at the widest point. When it comes to designing a solid body guitar the sky is the limit. Keep it traditional or get as wacky as you like. The shape of the body doesn’t affect the tone of the guitar as greatly as it does with acoustic guitars. These plans are based around a Les Paul-style guitar.
Cut the MDF templates out on the bandsaw and clean up the body and headstock profile on a spindle sander. To get perfectly straight neck edges, screw a piece of MDF (approx. 20' x 6') with a jointed edge to the neck template right along the pencil line of one edge. Use a flush trim template bit in the table router to trim the edge of the neck. Repeat on second edge. Clean up the end of the neck template with a disc sander.
Draw centerlines on both the neck and body templates. Drill index holes in the neck and body templates with a ¼' brad point. These index holes will be used to align and pin the templates to the wood for all machining processes. The body requires two index holes, on center, that need to be inside the neck pocket and inside the bridge pick-up cavity so they will be hidden. The neck template requires two index holes as well; positioned about 2' in from the heel end, and about 2' from the nut (toward the heel). Exact positioning is not critical, however, the holes must be far enough off center to be outside of the truss rod slot.
Master templates – Take care to make these templates carefully because they will be used repeatedly to machine the body and neck of the guitar.
Body Index template – In order to rout the neck pocket and pick-up cavities, the routing templates need index holes outside of the body profile, since there are no other places for concealable index holes on the top of the guitar. This will be the master from which all routing templates are based. Cut a piece of clear acrylic (plexi-glass) to 21'x 4'. Scribe a centerline the length of the piece with the back edge of an exacto knife. Clamp it to the body template to drill index holes. Drill a second set of index holes outside the body profile. These will be the index holes used for all body routing jigs.
Body index template – A number of jigs will reference off this template in order to keep the body free of holes.
Control Cavity/Cover plate recess routing template – Draw a centerline on a 21'x 14' piece of ¾' MDF. Making sure the centerlines are aligned, clamp the acrylic body index to the MDF as a drill guide. With a ¼' brad point, drill the inside and outside sets of index holes through the MDF. With ¼' steel pins, attach the body template to the MDF and trace the body profile. Mark your control layout on both sides of the centerline. On one side draw your control cavity, on the other side draw the cover plate. Drill out the center with a large forstner bit, then spindle sand to shape. Alternately, use a jigsaw to remove the waste before sanding to shape.
Cavities – The cavities are made by running a flush trim bit off of this pattern.
Neck Pocket routing template – Draw a centerline on a 21' x 10' piece of ¾' MDF. Clamp the acrylic body index to the MDF (centerlines aligned) as a drill guide. With a ¼' brad point bit, drill the inside and outside sets of index holes about15mm into the MDF. With ¼' steel pins, attach the body template to the MDF. Trace the body profile. Mark out the neck pocket (exact size of neck template).
Frame out the neck pocket with pieces of MDF that have been trued on one edge. Pre-drill and counter sink the MDF pieces, then screw them to the template. Check the fit with your neck template. With a ½' template bit, rout out the neck pocket. Remove the frame.
Frame it then route it – Create the framework with straight scraps. The router bit will follow this frame to produce the neck pocket.
Pick-up Cavity routing template – Draw a centerline on a 21'x 10' piece of ¾' MDF. Clamp the acrylic body index to the MDF (centerlines aligned) as a drill guide. With a ¼' brad point bit, drill the inside and outside sets of index holes about 15mm into the MDF. With ¼' steel pins, attach the master body template to the MDF. Trace the body profile and remove the template. Next, pin on the neck pocket template. Trace the neck pocket and remove the template. Mark out the pick-up cavities on the MDF pick-up routing template. Frame out the pick-up cavities with pieces of MDF that have been trued on one edge and fasten them to the template. With a ½' template bit, rout out the cavities. This is done in two steps to get the shape required; one pass wider and shorter, the second pass narrower and taller. Framing and routing the cavity as two separate rectangles, with four larger pieces of MDF, will produce a more uniform cavity than using eight smaller pieces and routing the cavity all at once.
Pick-up cavity, step one – Frame the cavity to be routed, then machine the first cavity.
Pick-up cavity, step two – Re-frame the cavity at a slightly different size and route out the material.
Ibanez Cavity Depth Definition

The Body
Begin by cutting your 8/4 body stock to 21' lengths (or longer depending on your body shape). Joint the best edge and bandsaw to at least 7 ½'. Joint one face. If you do not have a thickness sander, you will need to plane your stock to final thickness before glue-up. Standard thickness is about 41mm. If you choose to put a book-matched top on your guitar, the back should be about 35mm with a 5mm thick top.
The real deal – Use the template to rout the pick-up cavities in the body.
Glue up
Be sure your glue edges are true. Run a heavy bead of good quality wood glue down one edge and spread to cover the entire surface and clamp until dry. Use MDF cauls and C-clamps to keep the body halves flush. During glue up be sure to use wax paper or poly film between the cauls and the body blank! Once the body has dried for 24 hours, scrape the dried glue squeeze out and sand both faces clean and flat. Lay the body index template on the top face of the body and align the centerline with the glue line. Clamp it in position and drill the outside set of index holes with a ¼' brad point bit. Drill the inside set of index holes 10mm deep. Pin the body profile template to the body blank and trace the profile. Rout the pick-up cavities.
Pin the pick-up template to the body. Always use steel pins when routing.
With a ½' template bit, rout the cavities 20mm deep, in two or three passes. If you don’t have a plunge router, drill a starter hole to full routing depth with a forstner bit to allow the bit to plunge to full depth before routing.
Rout the Neck Pocket
Pin the neck pocket template to the body. With a ½' template bit, rout the neck pocket 15mm deep. Take at least two or three passes to slowly remove all the waste. Drill the control holes according to the shaft size of the pots/switches you’re using. They should be 10mm deep.
The neck is next – Continue routing, this time removing the waste to create the neck pocket.
Rout the Control Cavity
Pin the control cavity/cover plate recess template to the body. With a ½' template bit, rout the cover plate recess 4mm deep. Flip the template and push the pins through to the other side. Pin the template to the body and with multiple passes rout the control cavity 35mm deep. You may have to shim up your template to rout the cover plate recess, and remove the template to rout the full depth of the control cavity.
Carefully bandsaw the body profile and spindle sand to final shape.
Clamp the neck template into the neck pocket and measure out the bridge and tailpiece locations. The distance from the nut to the bridge is 24 ⅝' (treble side) and 24 13/16' (bass side). The tailpiece is 26 ¼' from the nut. Measurements are to the center of the post hole. The manufacturer of the hardware should specify post hole spacing. Drill the bridge and tailpiece holes.
Ease the edge of the body with a ¼' round over bit. Use your jack plate to mark and drill the jack mounting holes with a ¾' forstner bit. Drill the pilot holes for the strap pins. The pick-ups can be mounted with rings or straight to the bottom of the cavity without a ring. Mark and drill the pick-up mounting holes. I mount the pick-ups without rings.
Drill a hole for pick-up leads and ground wire. With a long ¼' bit, drill from the pick-up cavities to the control cavity. With a long ⅛' bit, drill from the treble side bridge hole to the control cavity. Use a piece of tubing over the bit to protect the edge of the tailpiece hole.
Sand the body to 400 grit.
In control – By now you’re getting the hang of things. Route the control cavity in the body
Careful layout is critical – Make sure the location of the holes is accurate. You don’t want any surprises later.
Drill for the jack – Clamp the body to a stable surface while you drill a ¾' hole to mount the jack.
Ibanez Cavity Depth Bass
Drill some holes – Drill the bridge and tailpiece holes.
Holes for Leads and wires – Drill holes for pick-up leads and ground wire with an extra long twist bit. Protect the wooden body by covering the bit with a piece of tubing.
For Part 2 of this article, click here.
Related Articles
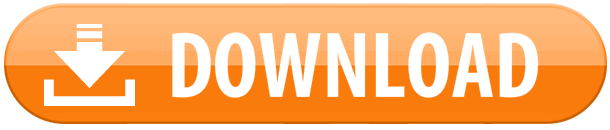